Laborausstattung
Thermische und Mechanische Analyse
Differential Scanning Calorimeter (DSC) messen Temperaturen und Wärmeströme im Zusammenhang mit thermischen Übergängen in einem Material.
Metallische Werkstoffe sind aufgrund ihrer physikalischen Eigenschaften oft besonders für die DSC-Analyse geeignet. Einige der wichtigsten Anwendungen bei metallischen Materialien sind:
- Schmelztemperatur und Schmelzverhalten: DSC kann dazu verwendet werden, die Schmelztemperatur von Metallen und Legierungen zu bestimmen und zu untersuchen, wie sich diese bei verschiedenen Legierungszusammensetzungen verändern.
- Phasenübergänge: Metallische Werkstoffe durchlaufen oft verschiedene Phasen (z.B. von fest zu flüssig oder von einer Kristallstruktur zu einer anderen). DSC hilft, diese Phasenübergänge präzise zu charakterisieren und zu quantifizieren.
- Reaktionen wie Oxidation oder Kristallisation: Metallische Materialien, insbesondere Legierungen, können während der Abkühlung Kristallisationsprozesse durchlaufen, die mit der Wärmeentwicklung oder -aufnahme verbunden sind. Diese Reaktionen können mittels DSC erfasst werden.
- Thermische Stabilität: Das DSC-Gerät kann dazu verwendet werden, die thermische Stabilität von Metallen oder Legierungen zu messen, insbesondere im Hinblick auf ihre Verwendung in Hochtemperaturanwendungen.
- Bestimmung der spezifischen Wärmekapazität: Die spezifische Wärmekapazität von Metallen kann durch die DSC-Messung ebenfalls ermittelt werden, was für die thermische Charakterisierung des Materials von Bedeutung ist.
- Untersuchung von Legierungszuständen: Bei der Entwicklung neuer Legierungen ist es wichtig, die thermischen Eigenschaften der verschiedenen Phasen und deren Stabilität unter Temperaturänderungen zu verstehen.
Flash DSC stellt eine leistungsstarke und präzise Technik zur Untersuchung schneller thermischer Prozesse in Materialien dar. Es ist besonders nützlich, wenn schnelle Messungen und minimale Probegrößen erforderlich sind, und wird daher häufig in der Forschung und Entwicklung von neuen Materialien und Produkten eingesetzt.
Funktionsweise von Flash DSC:
Im Gegensatz zu traditionellen DSC-Geräten, bei denen die Temperatur des Probenmaterials schrittweise über längere Zeiträume erhöht wird, erfolgt die Temperaturerhöhung bei Flash DSC in sehr kurzen Zeitspannen. Hier sind die wichtigsten Merkmale:
- Schnelle Temperaturänderung: Flash DSC arbeitet mit einer extrem schnellen Temperaturänderung (oft bis zu 1000 °C pro Minute oder mehr). Dies ermöglicht die Untersuchung von sehr schnellen thermischen Prozessen, wie z. B. Glasübergängen oder Schmelzprozessen, die bei herkömmlichen DSC-Geräten möglicherweise nicht in der benötigten Detailtreue erfasst werden können.
- Minimale Probegröße: Aufgrund der schnellen Heiz- und Kühlraten sind Flash DSC-Experimente oft mit sehr kleinen Proben (im Bereich von Mikrogramm bis Nanogramm) möglich. Das macht diese Technik besonders nützlich, wenn nur geringe Materialmengen zur Verfügung stehen oder wenn die Probe nicht zerstört werden darf.
- Schnelle Erfassung thermischer Übergänge: Mit Flash DSC können sehr schnelle thermische Übergänge, wie z. B. die Kristallisation von amorphen Materialien oder der Glasübergang, präzise erfasst werden. Diese Übergänge wären mit langsameren Messmethoden möglicherweise schwer zu detektieren oder würden weniger präzise Ergebnisse liefern.
Anwendungen von Flash DSC:
Flash DSC wird in verschiedenen Bereichen eingesetzt, insbesondere in der Materialwissenschaft, der Polymerforschung und der Chemie. Zu den typischen Anwendungen am LMW gehören:
- Materialwissenschaften: Bestimmung des Glasübergangs (Tg), der Kristallisationstemperatur (Tc) oder der Schmelztemperatur (Tm) von Metallischen Gläsern.
- Dünnschichtsysteme: Analyse von thermischen Übergängen in dünnen Filmen, bei denen schnelle Veränderungen von Bedeutung sind.
- Materialcharakterisierung: Untersuchung von amorphen metallischen Legierungen auf schnelle thermische Phänomene.
Vorteile von Flash DSC:
- Hohe Auflösung: Da die Temperaturänderung sehr schnell erfolgt, können kleine thermische Übergänge mit hoher Präzision gemessen werden.
- Energieeffizienz: Flash DSC benötigt weniger Zeit und Material im Vergleich zu traditionellen DSC-Verfahren.
- Vielseitigkeit: Die Technik ist für eine Vielzahl von Materialien und thermischen Prozessen geeignet, einschließlich solcher, die mit herkömmlichen DSC-Techniken schwer messbar sind.
Die Differentielle Thermoanalyse (DTA) ist das meistgenutzte thermische Verfahren zur Materialanalyse. Die DTA nutzt die Tatsache eines charakteristischen Energieumsatzes beim Phasenübergang zur qualitativen und quantitativen Analyse. Die Messung basiert auf einem Vergleich der Probentemperaturen mit einer Referenz. Die Geräte werden zur Charakterisierung von Pharmazeutika, Lebensmitteln, Chemikalien und anorganischen Substanzen verwendet, gemessen werden Glasumwandlungen, Kristallisation, Schmelzen und Sublimation.
Durch die vakuumdichte Bauweise sind Messungen der Enthalpie mittels verschiedenen Öfen, Messsystemen und Tiegeln in einem Temperaturbereich von -150°C bis 1600°C unter saubersten Atmosphären sowie unter Vakuum von 10E-5 mbar möglich.
Bei metallischen Werkstoffen wird die DTA häufig verwendet, um:
- Phasenübergänge wie Schmelz-, Erstarrungs- oder Umwandlungstemperaturen zu bestimmen.
- Wärmebehandlungsprozesse zu überwachen und zu optimieren, z. B. in der Stahl- und Aluminiumindustrie.
- Thermische Stabilität von Legierungen zu bewerten und deren Reaktionsverhalten bei verschiedenen Temperaturen zu analysieren.
- Konditionierung von Werkstoffen zu optimieren, z. B. beim Alterungsprozess von Legierungen.
TMA (Thermal Mechanical Analyzer) untersucht das thermomechanische Verhalten eines Materials, d. h. die Veränderung der mechanischen Eigenschaften (z. B. Ausdehnung, Verformung) in Abhängigkeit von der Temperatur.
Bei metallischen Werkstoffen wird ein TMA-Experiment häufig eingesetzt, um spezifische Materialeigenschaften zu bestimmen, die unter Temperatureinfluss variieren können. Diese Versuche geben Aufschluss über das Verhalten eines Metalls im Bereich von Temperaturänderungen und helfen, wichtige Eigenschaften wie:
- Thermische Ausdehnung (Thermal Expansion)
- Weichwerden oder Verformungstemperatur (z. B. die Temperatur, bei der ein Metall plastisch wird)
- Phasenübergänge wie Schmelzen oder Kristallisation
- Elastizitätsmodul und Festigkeit bei erhöhten Temperaturen
- Viskositätsverhalten nahe des Glasübergangs.
Anwendungen des TMA bei metallischen Werkstoffen:
- Bestimmung der Temperatur, bei der plastische Verformung einsetzt: Dies ist für Metallische Gläser von Bedeutung, die in Prozessen wie dem thermoplastischen Formen verwendet werden, um die Temperaturbedingungen optimal zu steuern.
- Untersuchung der Phasenübergänge: TMA kann dabei helfen, die Phasenübergänge (z. B. von Festkörper zu Flüssigkeit oder Kristallisation) genau zu bestimmen.
- Messung von mechanischen Veränderungen bei unterschiedlichen Temperaturen: Dies ist besonders relevant bei der Untersuchung der Leistungsfähigkeit von Werkstoffen unter unterschiedlichen Temperaturbedingungen.
- Analyse der Materialstabilität: In vielen Anwendungen, wie in der Luftfahrt- oder Automobilindustrie, sind Werkstoffe extremen Temperaturwechseln ausgesetzt. Das TMA hilft, das Verhalten des Materials bei unterschiedlichen thermischen Belastungen zu evaluieren, um den kritischen Anwendungsbereich festzulegen.
Ein Rotationsviskosimeter ist ein Instrument, das zur Messung der Viskosität von Flüssigkeiten verwendet wird. Bei der Untersuchung von metallischen Werkstoffen, die in flüssiger Form vorliegen, wie z. B. beim Schmelzen von Metallen oder in bestimmten Prozessen der Metallbearbeitung, ist die Viskosität eine wichtige Größe, da sie das Fließverhalten der Schmelze beschreibt.
Anwendung bei metallischen Werkstoffen:
- Untersuchung von Metall-Schmelzen;
- Spezielle Legierungen und Schmelzen mit additiver Fertigung.
Wichtige Aspekte bei der Messung der Viskosität von metallischen Schmelzen:
- Temperaturabhängigkeit: Die Viskosität metallischer Schmelzen ist stark temperaturabhängig und sinkt in der Regel mit steigender Temperatur. Dies muss bei der Messung berücksichtigt werden.
- Legierungszusammensetzung: Verschiedene Legierungen weisen unterschiedliche Viskositäten auf, was durch die Zugabe von Legierungselementen (z. B. Kohlenstoff, Silizium) beeinflusst wird.
- Verunreinigungen: Verunreinigungen in der Schmelze (wie Oxide oder Schlacke) können die Viskosität ebenfalls erhöhen, was eine exakte Kontrolle erfordert.
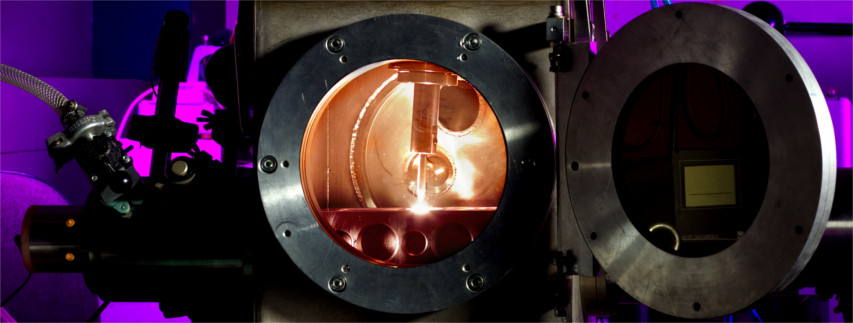
Legierungherstellung und Verarbeitung
Lichtbogenöfen (auch Elektrolichtbogenöfen oder EAF für "Electric Arc Furnace") sind spezielle Schmelzöfen, die in der Metallverarbeitung eingesetzt werden, um Metalle, insbesondere Stahl, durch den Einsatz von elektrischen Lichtbögen zu schmelzen. Sie kommen vor allem in der Stahlindustrie zum Einsatz, um Rohstahl aus Stahlschrott zu gewinnen, aber auch in anderen Bereichen der Metallproduktion, wie etwa in der Aluminium- oder Kupferverarbeitung.
Der Lichtbogenofen wird in unserem Labor zur Herstellung von hochreinen metallischen Legierungen unter Schutzgas verwendet. Die hergestellten Legierungen besitzen eine hohe Qualität und ermöglichen es zuverlässig die speziellen Werkstoffeigenschaften verschiedenster, eigens hergestellter Materialien zu bestimmen.
Funktionsweise von Lichtbogenöfen:
Ein Lichtbogenofen nutzt elektrische Lichtbögen, die zwischen Wolframelektroden und dem zu schmelzenden Material gebildet werden. Der Lichtbogen erzeugt eine enorme Hitze (bis zu 3.000 °C), die notwendig ist, um auch hochschmelzende Metalle legieren zu können.
In unseren Anlagen wird der Schmelzvorgang unter Schutzgasatmosphäre durchgeführt.
- Erzeugung des Lichtbogens: Die Bestandteile der gewünschten Legierung werden in Form von kleinen Stücken bzw. Pulver in eine Kupfermulde gelegt. Anschließend wird der Lichtbogen gezündet und über die Mulde mit den Legierungsbestandteilen geführt, wobei der Lichtbogen diese Bestandteile vollständig aufschmilzt. Der Vorgang wird wiederholt bis eine homogene Einheit der Legierung erreicht wird, (die bei uns die Form eines metallischen Knopfes hat).
- Probenherstellung: Nach dem Schmelzen wird dieser entstandene metallische Knopf als Ausgangsmaterial für die Herstellung von Proben in nachgelagerten Gussverfahren zur Bestimmung der Materialeigenschaften oder zur Weiterverarbeitung in den anderen Anlagen verwendet.
Sauggussanlage (Vakuumgussverfahren)
Die Sauggussanlage ist eine spezielle Gießtechnik, bei der durch einen Unterdruck ein flüssiges Metall in eine gekühlte Form gesaugt wird, um eine hohe Qualität und Präzision des Gussstücks bei sehr hoher Kühlung zu erreichen. Das Verfahren wird hauptsächlich zur Herstellung von hochpräzisen, fehlerfreien Gussstücken genutzt, die oft in anspruchsvollen Industrien wie der Luft- und Raumfahrt, Medizintechnik und der Automobilindustrie eingesetzt werden.
Funktionsweise:
- Vakuum erzeugen: Ein Vakuum wird erzeugt, um Luft und Verunreinigungen aus der Gießform zu entfernen. Dies minimiert Gaseinschlüsse und poröse Stellen im Gussstück. Die Gießform in unseren Anlagen ist eine Kokille aus Kupfer, in die die gewünschte Form eingebracht wurde.
- Metallgießen: Das zu gießende Metall wird zuerst mittels Lichtbogen im muldenförmigen oberen Teil der Kokille aufgeschmolzen. In der Anlage oberhalb der Kokille herrscht leichter Überdruck durch ein Schutzgas. Sobald das Metall flüssig ist, wird im unteren Teil der Kokille durch Öffnen des Ventils ein Vakuum angelegt, welches mit Hilfe des Überdrucks das Metall in die Form saugt. So fließt das Metall auch in schwer zugängliche Bereiche der Form.
- Abkühlen und Entformen: Nach dem Gießen kühlt das Metall rapide ab und erstarrt in der Form.
Kippgussanlagen sind klassische Gießanlagen, die in der Metallverarbeitung und -produktion zur Umformung von Metallen verwendet werden, um Metalle in verschiedensten Formen herzustellen. Diese Anlagen zeichnen sich durch die Möglichkeit aus, das Gießverfahren durch Kippen der Gießform oder des Schmelzbehälters zu steuern. Diese Technik wird oft in der Herstellung von Gussteilen für verschiedene Industrien wie Automobilbau, Maschinenbau und Medizintechnik eingesetzt. Die Kippgussverfahren erlauben eine präzise Kontrolle über den Fluss des geschmolzenen Metalls und bieten Vorteile in Bezug auf die Qualität der Gussteile, insbesondere bei der Herstellung komplexer Geometrien.
Kippgussverfahren:
Im Kippgussverfahren wird der Schmelzofen oder die Gießform geneigt, um das flüssige Metall in die Form zu gießen. Dies kann entweder durch manuelles Kippen oder durch ein automatisiertes System erfolgen. Je nach Anwendung können Kippgussanlagen in verschiedenen Größen und für unterschiedliche Materialien konzipiert werden.
Es ist eine industrielle Fertigungsanlage, die speziell darauf ausgelegt ist, sowohl thermoplastische Kunststoffe als auch metallische Werkstoffe zu verarbeiten und zu formen. Solche Anlagen kommen in verschiedenen Branchen zum Einsatz, darunter der Automobilbau, die Luft- und Raumfahrt, die Elektronikindustrie und die Herstellung von Maschinenbaukomponenten. Sie kombinieren unterschiedliche Technologien, um eine breite Palette von Materialien und Formen zu produzieren.
Haupttechnologien und Prozessschritte in einer solchen Anlage:
1. Thermoplastisches Formen (z. B. Spritzgießen, Extrusion, Thermoformen)
- Unter Schutzgasatmosphäre werden die metallischen Glas Proben zwischen zwei erhitzten Stempeln durch Druck in eine Form gepresst. Nach dem Pressen werden diese Proben dann rasch abgekühlt und erstarren in der Form.
2. Verarbeitung von metallischen Werkstoffen (z. B. Gießen, Schmieden, Walzen)
- Schmieden: Metall wird in einem Schmiedebereich durch mechanische Arbeit (z. B. Hämmern oder Pressen) bearbeitet, um es in die gewünschte Form zu bringen.
- Walzen: Metall wird durch Walzen in dünne Bleche oder andere Formen umgewandelt.
Eine Walze ist ein Werkzeug oder eine Maschine, die in der Metallbearbeitung verwendet wird, um Materialien zu formen oder zu bearbeiten. Walzen können verschiedene Formen annehmen, je nachdem, welcher Prozess durchgeführt wird.
- Walzen im Metallumformungsprozess: In der Umformtechnik bezieht sich "Walzen" auf den Prozess, bei dem Metall durch Rollenzwischenräume gepresst oder gezogen wird, um es in Form zu bringen. Beispiele sind das Walzen von Blechen, Stahl, Aluminium oder anderen Metalllegierungen. Dieser Prozess ist besonders für die Herstellung von Blechen, Drähten und Profilen wichtig.
- Walzen in der Praxis: Walzen wird in der Stahl- und Aluminiumindustrie häufig genutzt, um Rohmaterialien in verschiedene Formen wie Bänder, Platten oder Drähte zu bringen. Walzen kann auch in verschiedenen Varianten wie Profilwalzen oder Schrägwalzen erfolgen.
Schleif- und Poliermaschinen spielen eine entscheidende Rolle in der Analyse neuer Materialien, insbesondere wenn es um die tiefgehende Analyse der Mikrostruktur und der resultierenden spezifischen Werkstoffeigenschaften geht.
Doppelschleifmaschinen wie PRESI Mecatech 250 bieten eine stabile Grundlage und sind ideal für präzise Schleifvorgänge. Sie kommen oft in der Metallbearbeitung zum Einsatz und bieten eine gute Kombination aus Abtragleistung und Oberflächenfinish.
Die Wahl der Schleif- oder Polierprozedur hängt maßgeblich von den Werkstoffeigenschaften des Materials ab, das bearbeitet werden soll. Harte, zähe Materialien erfordern leistungsstärkere Maschinen und robusteres Schleifwerkzeug, während weichere oder empfindlichere Materialien schonender bearbeitet werden müssen. Wichtig ist auch die Auswahl des richtigen Schleifmittels und die Anpassung der Bearbeitungsparameter (z. B. Drehzahl, Anpressdruck, Kühlung), um das gewünschte Ergebnis zu erzielen.
Eine Präzisions-Trennmaschine ist ein spezialisiertes Gerät, das für das präzise Schneiden oder Trennen von Werkstoffen, insbesondere von metallischen Materialien, entwickelt wurde. Sie kommen besonders bei der Charakterisierung von metallischen Werkstoffen zum Einsatz, um Materialproben mit möglichst wenig beeinflusstem Gefüge zu gewinnen.
Hier einige typische Anwendungen:
- Analyse von Metallkomponenten: Präzises Trennen von Metallplatten, -stäben oder ganzen Baugruppen von Teilen für Maschinen, Autos oder Flugzeuge, teilweise auch zur Schadensanalyse von versagenden Teilen.
- Zerlegen von Werkstücken für weitere Bearbeitungsschritte: Zum Beispiel beim Schneiden von Metallproben für Prüfungen oder bei der Herstellung von Schnittmustern für Gussteile.
In der Praxis erfolgt der Schnitt bei niedrigen Schnittgeschwindigkeiten, wobei oft spezielle Diamantsägeblätter und Korund- oder SIC-Trennscheiben unter konstanter Wasserkühlung verwendet werden, die auf die spezifischen metallischen Werkstoffe und Anforderungen abgestimmt sind.